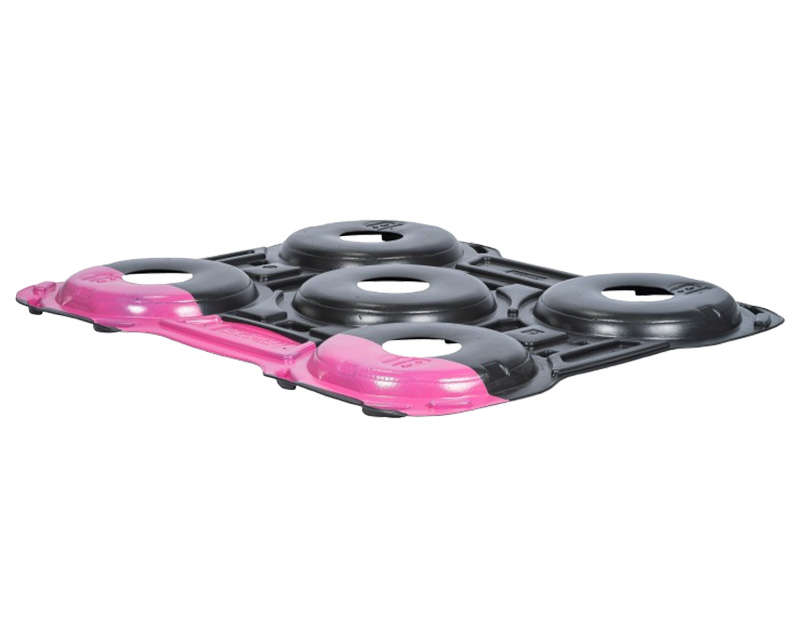
Benefits of Wheel Separator Trays
Wheel separator trays offer many benefits for logistics processes, especially when the focus is on efficiency and protecting the products being transported.
They are made from high-quality materials, such as HDPE, which guarantee strength and durability.
One of the main advantages is that the trays are returnable, meaning they can be reused several times, reducing costs with disposable packaging.
Their recyclability provides a significant environmental benefit, as it contributes to the sustainability of logistics processes. The trays are also washable, which makes maintenance easier and prolongs their useful life.
Another important benefit is the stackability of the trays, which are fully interlocking, allowing for compact storage, which optimizes space and facilitates organization in warehouses and transport areas.
The presence of drainage holes is also a plus, as it prevents the accumulation of water, preventing damage to the wheels and guaranteeing the preservation of product quality during transportation and storage.
The trays are resistant to low temperatures and can be used in environments with temperatures as low as -35ºC, making them extremely versatile.
Additional Information
Wheel separator trays are designed to meet the specifications of different types of wheels, from automotive to agricultural wheels. They are available in several models, such as wheel separators for 14", 15", 16", 17", 17.5", 18", 19" and 22.5".
There are specific models for agricultural wheels from 16" to 42", depending on the customer's needs. Each tray is manufactured with certified HDPE material, which ensures compliance with the standards required for the automotive industry, as well as other sectors.
In addition to the standard colors (black and white), the trays can be customized with other colors, such as green, blue, gray and yellow, upon request.
This customization possibility also extends to the optional colored band, which can be applied to help identify and organize the trays.
Wheel separator trays are widely used in the transportation of raw or machined wheels, making them an ideal solution for reverse logistics and the efficient transportation of heavy and bulky parts.
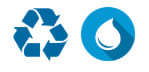
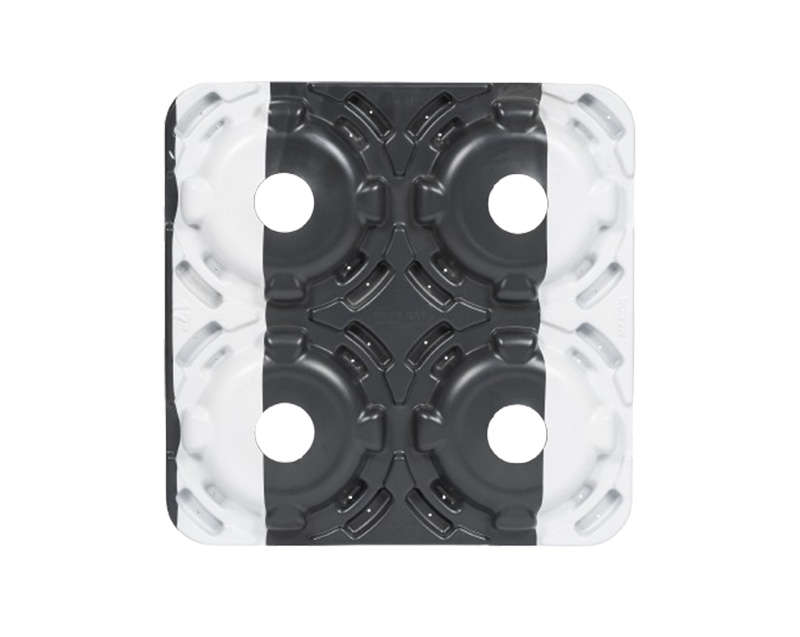
Wheel Separator Trays - Technical Specifications
MODEL | FEATURES | DIMENSIONS | CAVITIES | APPROX. WEIGHT | INITIAL THICKNESS | OPTIONAL ACCESSORIES |
---|---|---|---|---|---|---|
14" WHEEL SPACER | HDPE | 1200 X 1115 mm | 8 | 3.2 kg | 2.5 mm | RANGE |
15" WHEEL SPACER | HDPE | 1360 x 1145 mm | 8 | 3.8 Kg | 2.5 MM | RANGE |
16" WHEEL SPACER | HDPE | 1195 x 1105 mm | 5 | 3.2 kg | 2.5mm | RANGE |
17" WHEEL SPACER | ||||||
HDPE | 985x 985 mm | 4 | 3.2 kg | 4.0 mm | RANGE | |
HDPE | 1195x1105 mm | 5 | 3.2 Kg | 2.5 mm | RANGE | |
17.5" WHEEL SPACER | HDPE | 1210x1210 mm | 5 | 3.4 Kg | 2.5 mm | RANGE |
18" WHEEL SPACER | HDPE | 1370X1180 mm | 5 | 2.35 Kg | 1.5 mm | RANGE |
18" WHEEL SPACER | HDPE | 1370X1190 mm | 5 | 2.35 Kg | 1.5 mm | RANGE |
19" WHEEL SPACER | HDPE | 1200X1200 mm | 4 | 3.3 Kg | 2.5 mm | RANGE |
22.5" WHEEL SEPARATOR | HDPE | 1210x1210 mm | 4 | 3.4 Kg | 2.5 mm | RANGE |
16", 18", 32" and 38" WHEEL SEPARATOR - TWIN SHEET | HDPE | 1145 X 1145 mm | 4 | 10.0 Kg | 4.0 mm | - |
WHEEL SEPARATOR 24"- 26" - 28"- TWIN SHEET | HDPE | 775 x 795 mm | 1 | 4.6 kg | 4.0 mm | - |
Frequently Asked Questions about Wheel Separator Trays
The market offers different types of wheel separators, each designed to meet specific needs.
Among the most common are the HDPE wheel separator and the polyion separator. The corrugated plastic separator is also a widely used alternative, especially for wheels of varying sizes.
The trays can be manufactured with different processes, such as single-sheet or twin-sheet, and in nestable models, which facilitates storage and optimizes space in logistics areas.
The use of spacers offers several advantages in the process of transporting and storing wheels. They guarantee extra protection for the parts, preventing damage caused by friction and impact.
Wheel separator trays are returnable and recyclable, which makes them more sustainable and economical, contributing to waste reduction.
Resistance to adverse weather conditions, such as extremely low temperatures, and ease of maintenance are also important advantages, since the trays can be washed and reused several times.
The most common materials used in the manufacture of wheel separators are HDPE (High Density Polyethylene) and polystyrene.
HDPE is widely used due to its durability, impact resistance and recyclability properties, making it a sustainable and economical option.
Polyionda is a lighter but equally strong material, making it ideal for smaller wheels or for applications where weight reduction is a priority.
Corrugated plastic is another alternative, often used to give trays more rigidity while maintaining a balance between strength and flexibility.
Choosing the ideal separator depends on several factors, such as the size of the wheels, the type of transport and the storage requirements.
If the aim is to transport smaller automotive wheels, such as 14" to 17", single-sheet models may be the most suitable choice, as they are lighter and easier to handle.
For larger wheels or agricultural use, twin-sheet models are more robust and offer greater stacking capacity.
It is important to consider the material of the separator, such as HDPE, which offers greater durability, or polyionda, which can be a more economical and lighter option.
Wheel separators, including the polyfoam separator and the corrugated plastic separator, can be purchased directly from specialized manufacturers or distributors of packaging and logistics solutions.
PLM offers products with certification and quality assurance, as well as customized options according to the specific needs of each client.
For those looking for a practical and efficient solution, PLM is the best option, guaranteeing products with high durability and a good cost-benefit ratio.
The maintenance of wheel separator trays is simple and essential to ensure their longevity and functionality.
As they are washable, the maintenance process consists mainly of regular cleaning to remove residues and prevent dirt from accumulating.
In addition, it is important to check for structural damage, such as cracks or breaks, especially in trays that are stacked or moved frequently. Regular inspection helps to identify possible problems before they affect operation.
By keeping the spacers well maintained, you ensure greater efficiency when transporting and storing the wheels.